CLT is one of the most energy-efficient building materials, and although there are several award-winning Self Builds in Britain that feature CLT, the growth of self builders using this solution in the UK is markedly slow. CLT is renowned for its low carbon footprint, strength-to-weight ratio, speed and ease of construction, which in theory provides a very tempting alternative for self builders aiming for a quick and low energy construction.
The direct precursor of CLT can be seen in a German system known as Brettstapel. It embraces the idea of stacking timber planks known as lamellas together by using nails. This method, developed in the 1990s, is still popular in Germany and Austria. The difference between CLT and Brettstapel is that CLT uses high-grade timber stacked in a cross pattern to provide structural strength across two axes, rather than stacking in a single direction. It is formed of layers of kiln-dried spruce or pine boards which are bonded together at 90 degrees using polyurethane adhesive.
When exposed to immense hydraulic pressure, large, stiff, dimensionally stable panels are formed. These can be up to 3.50 metres in width and 20 metres in length and can create the complete superstructure of a building.
Three visual qualities of CLT are available, these are: non-visual, industrial visual and high-grade visual. Non-visual is designed to be plasterboarded over, and industrial and high-grade visual are intended to be left exposed – usually for exposed soffits and high-grade for walls.
WHAT ARE THE BENEFITS OF CLT?
The accuracy achieved in the design of the panels is one of the main advantages of CLT. This is achieved by the use of Computer Numerical Control (CNC) machines which cut the panels using data from 3D CAD drawings. They are then delivered to the site and installed by CLT installers. The panels are created to such high degrees of accuracy that glazing for windows can be ordered from initial drawings.
The precision of CNC machines also improves the level of airtightness and thermal performance which means that CLT can be used in Passive House design. The added insulation required would be approx. 250mm, to achieve a value of 0.10 W/m2. CLT is a very eco-friendly construction method from a managed sustainable source, providing a positive CO2 balance.
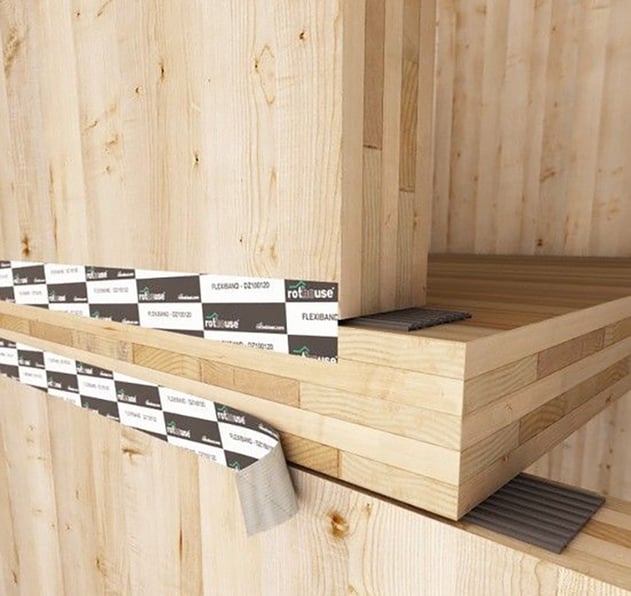
Building a house using CLT is quick, clean and the panels are easy to assemble on-site. Stora Enso, a renewable material company estimates that a detached CLT three-bedroom house can be built in five to eight days.
The speed of this construction method can help a self-builder to maintain financial liquidity, as key milestones for mortgage payments will be reached in less time, and thus the mortgage stage payment will be released sooner.
Another advantage of CLT is reduced foundation design compared to some other build methods, so it will save you time and money.
In regards to the aesthetic qualities of a build, if you choose to leave the internal timber surface exposed, you will achieve a striking contemporary timber interior with increased air quality. CLT also makes it easier to make design alterations as each wall has an associated drawing.
WHAT ARE THE DISADVANTAGES OF CLT?
The main problem with CLT is that there are currently no CLT manufacturers in the UK. This means that if you want to build your house with this material, you need to import it from Europe (the majority of CLT manufacturers are based in Austria). This will result in increased costs for the transportation of the materials. CLT is also more expensive than steel or concrete.
One full truck of CLT panels may be used to build an average to small house (40-50m3 of CLT). However, many of the CLT producers own or cooperate with British installers who provide CLT-related services.
As with any factory-manufactured method, the self-builder will need to ensure that the site can provide sufficient access for an articulated lorry and mobile crane. Once the CLT superstructure has been installed, another company will need to be employed to fix the external insulation of the house.
HOW MUCH DOES BUILDING A CLT HOUSE COST?
This question is not easily answered, as the cost is greatly influenced by the efficiency of the design. However, you can expect to pay somewhere between £350-£500/m2 of gross internal floor area for a CLT house. This may sound quite pricy, but there will be savings made through the speed of the build compared with other building methods.
Many CLT companies will provide an estimate of the cost of your project if you provide them with your drawings. This will include supply, design and installation of the CLT structural frame, but not the cost of the entire house.
CAN I GET A MORTGAGE FOR A CLT SELF BUILD?
CLT Self-build projects will be classed as a modern method of construction and as an off-site manufactured timber frame system, it should not be difficult to find a specialist Self Build lender for the project.
Self Build mortgage specialist, Tom McSherry from Buildstore advises that when building a house with an off-site system, the payment terms for the system are most, if not all, costs have to be paid in advance. It is crucial to ensure that the mortgage product used can provide the cashflow at the correct time to ensure these payment terms can be met.
When you apply for a mortgage, remember to provide full system’s details along with any BBA certifications which may be needed by the mortgage provider and make sure that the latent defects insurance policy covers off-site construction.
WHAT IS THE FUTURE FOR CLT IN THE UK?
Until a UK-based CLT manufacturer appears, it is unlikely to expect dramatic changes in prices in the near future. There is a possibility that using Sitka spruce (around 50% of the UK’s softwood resource) may be a viable proposition for manufacturing CLT in Britain.
However, some of the challenges of this solution are that it has a different performance to other softwoods in the continent under structural testing. They also need to be kiln-dried to a lower moisture content than current UK standards to match European CLT’s material properties.
If CLT’s popularity in the commercial sector continues to grow, there is potential that it can become popular in the custom build sector and be used more often to build low-energy modular homes. Although CLT is still not a very popular method among self builders, there are no doubts that it deserves some consideration when aiming for a highly efficient, design-led and structurally stable Self Build.