There is a set of basic design principles (or rules) you must follow to achieve a Fabric First design. At the heart of your self-build design will be a highly insulated building envelope with limited cold bridges and high-specification windows and doors. You need to use airtight membranes and tapes to limit air leakage from your building at all construction junctions. The next thing you need is to install an MVHR system, this will provide fresh heated air throughout the home. In order to maximise the sun’s natural solar gains, you have to make sure that the house’s design and orientation make the best use of the site. Finally and only once you have got the fabric bit right – you start looking at the renewable heating options.
Now that we know about the basics, we will focus on its six key elements in a bit more detail:
Many different construction types will provide an airtight, low-energy house, but some construction methods achieve it in a simpler, more cost-effective way. You need to choose a construction type which is naturally airtight, highly insulated and ideally produced in a factory environment rather than on-site. We recommend you choose one of the following types, all can easily achieve a u-value of 0.10 to 0.15 W/m2k:
Timber frame – Although it is a traditional construction method, it is cost-effective and can be easily used to achieve a low-energy house. It is advised to add extra airtightness membranes and external insulation.
Structural Insulated Panels (SIPs)– A rigid system with insulation bonded to OSB. This is a very airtight product.
Insulated Concrete Formwork (ICF) – An effective product for achieving an air-tight low-energy house. When using ICF you create a large area of thermal mass.
The thermal mass in ICF will effectively store the heat during the day and then release it throughout the night. Material with low thermal mass will just transfer heat, instead of storing it. If you use timber frame or SIPs, you can compensate for this lack of mass by using the concrete floor slab. If you design your building correctly to the Fabric First principles, you may only need to heat the ground floor, with no heating required on the first floor.
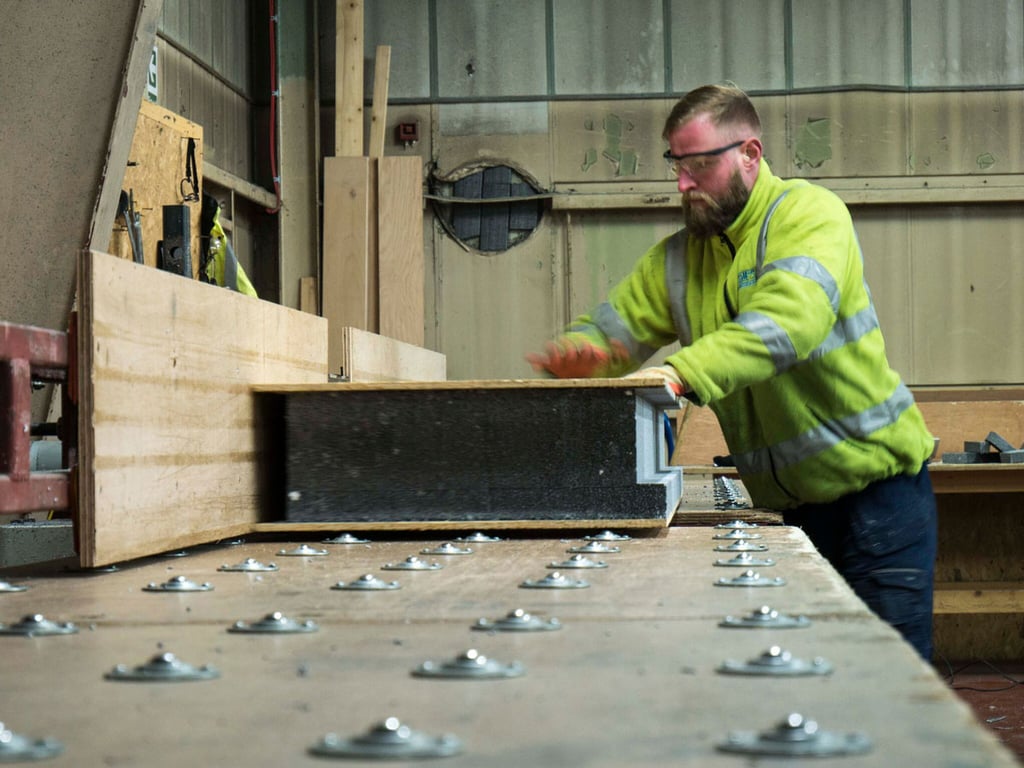
Firstly, let us put to rest one common misconception about airtight homes. Many people think: ‘I have got an airtight house, so I must close my windows and doors all the time’ – this is not true! In a Passive House the method of ventilation in summer is purge ventilation i.e. opening your windows or doors.
To increase airtightness, we advise that you tape the junctions of the panels on the external walls. Also, tape around the windows and door reveals. Then, you can wrap the whole building in an airtight membrane (increasing the airtightness of a Timber frame construction type). It is important to communicate to all the workers on your site, that if they need to make a hole in the building, they need to advise you so that you can seal it. Remember, that the squidgy foam used around the windows has no airtightness, so those areas have to be taped with the correct products.
For more information about the importance of airtightness, click here
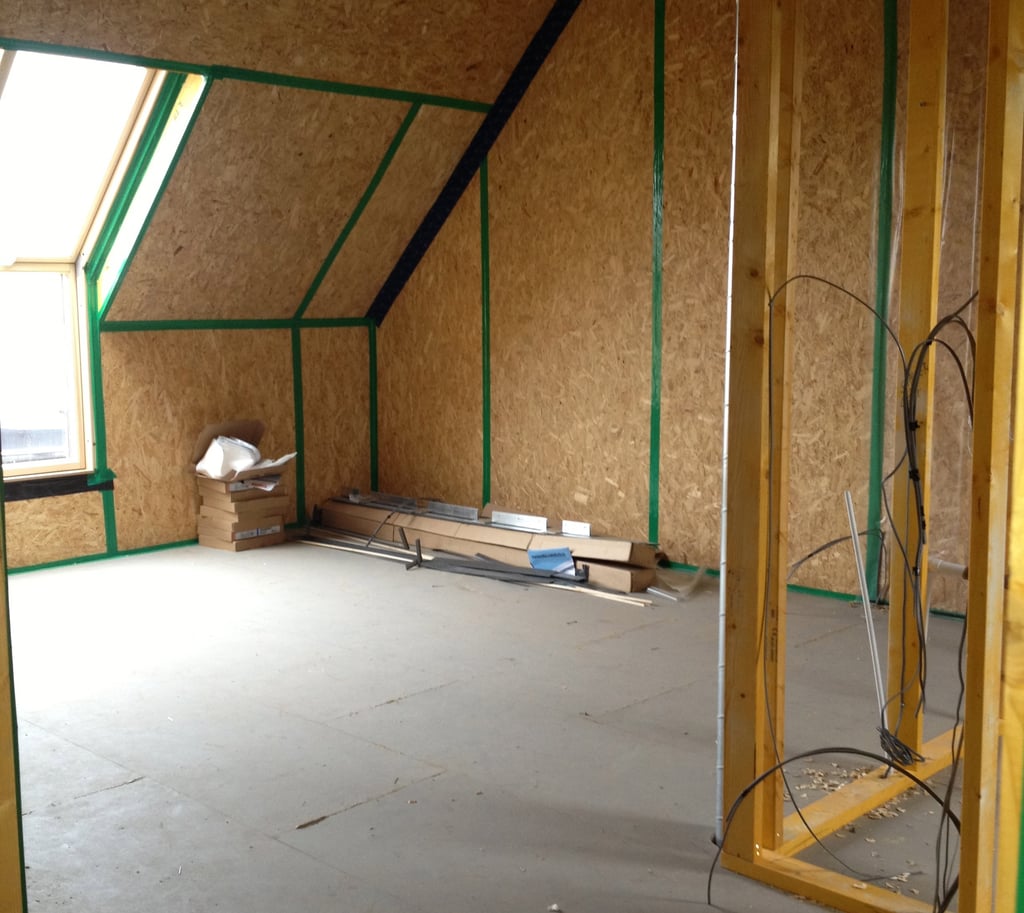
3 – LIMIT COLD BRIDGING
Cold bridges or thermal bridges are areas where construction elements have direct contact from the inside to the outside, for example, a timber batten in an external wall. These elements are usually poorer-performing elements and can create heat transfer through the building. So, if you want to have an energy-efficient house, you need to eliminate or reduce cold bridging as much as you can. One easy way to reduce this is to go from Timber frame construction to SIPS, as the SIPS construction has twice as few poor-performing timber battens (timber batten centres are generally 600mm and SIPS are 1200mm) To achieve a design where thermal bridges are limited, your architect will need to detail all of the major construction elements.
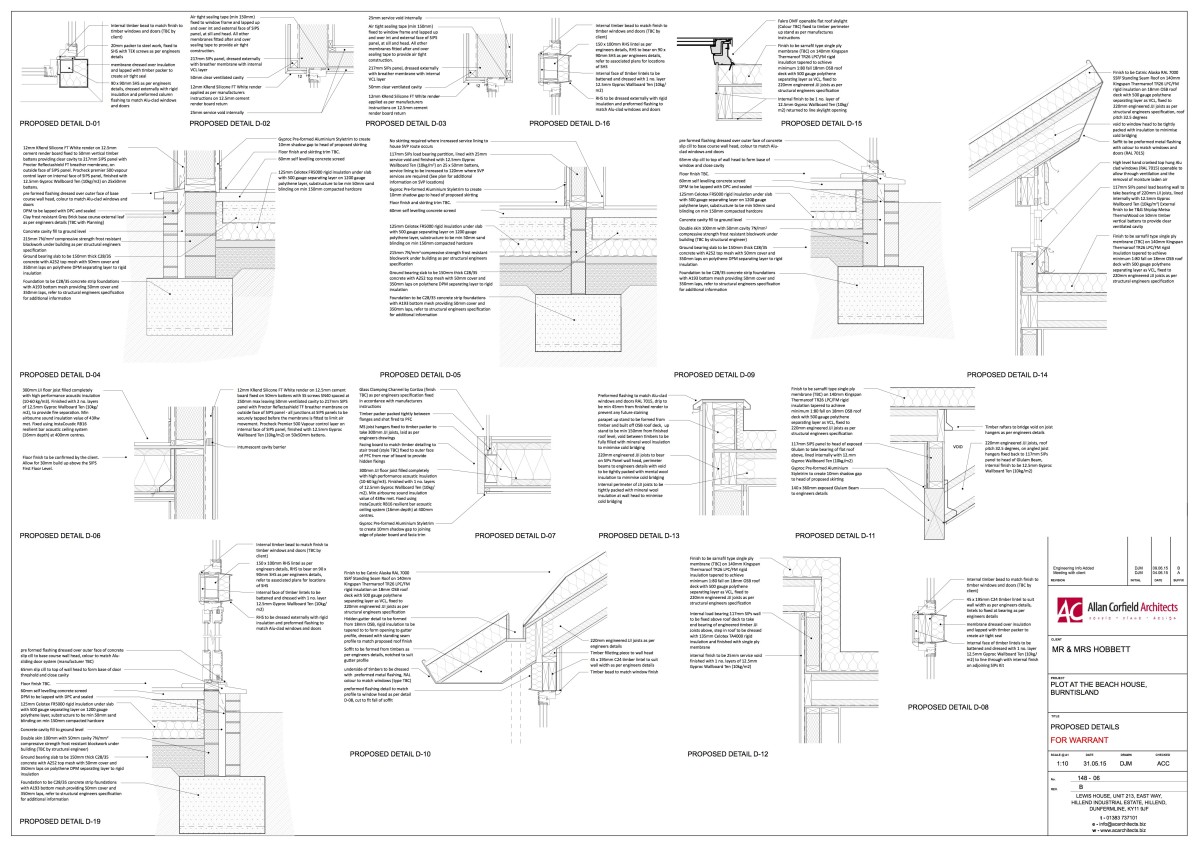
If you want to create an airtight house you have to manage the ventilation, You cannot just rely on the old-fashioned trickle vents. Traditionally, windows have little holes with plastic covers in the top frame, We open and close them to bring cold air into our house – It is impossible to manage this process.
However, with a heat recovery system, you can manage and control the amount of heated air which is moved around the house. It allows you to recirculate the air up to 10 times more than through trickle ventilators, which means much cleaner air in your self-build home. A Mechanical Ventilation with Heat Recovery (MVHR) system is usually recommended when you are planning to build a low-energy home, but it is important to make sure that you have appointed a professional to install and commission it.
For more information about MVHR systems, you can read our article here.
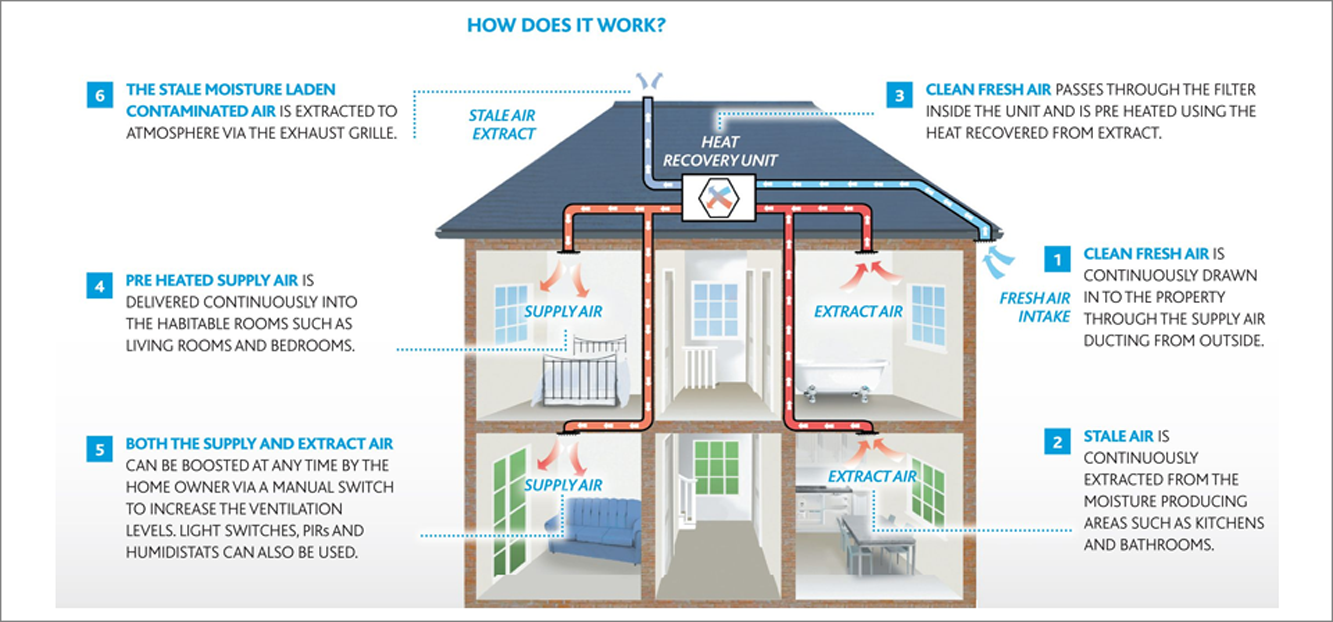
The next crucial part of designing a low-energy house is solar gain. It is important to correctly orientate the building, ensuring there are large openings on the southerly windows, with smaller openings on the north side. It may not be practical to design all your views to the south, but you need to have a trade-off between how energy efficient you want to be and making the most of your views. We would also recommend you consider accommodation of shading or brise soleil as (even) the UK can experience overheating during the summer.
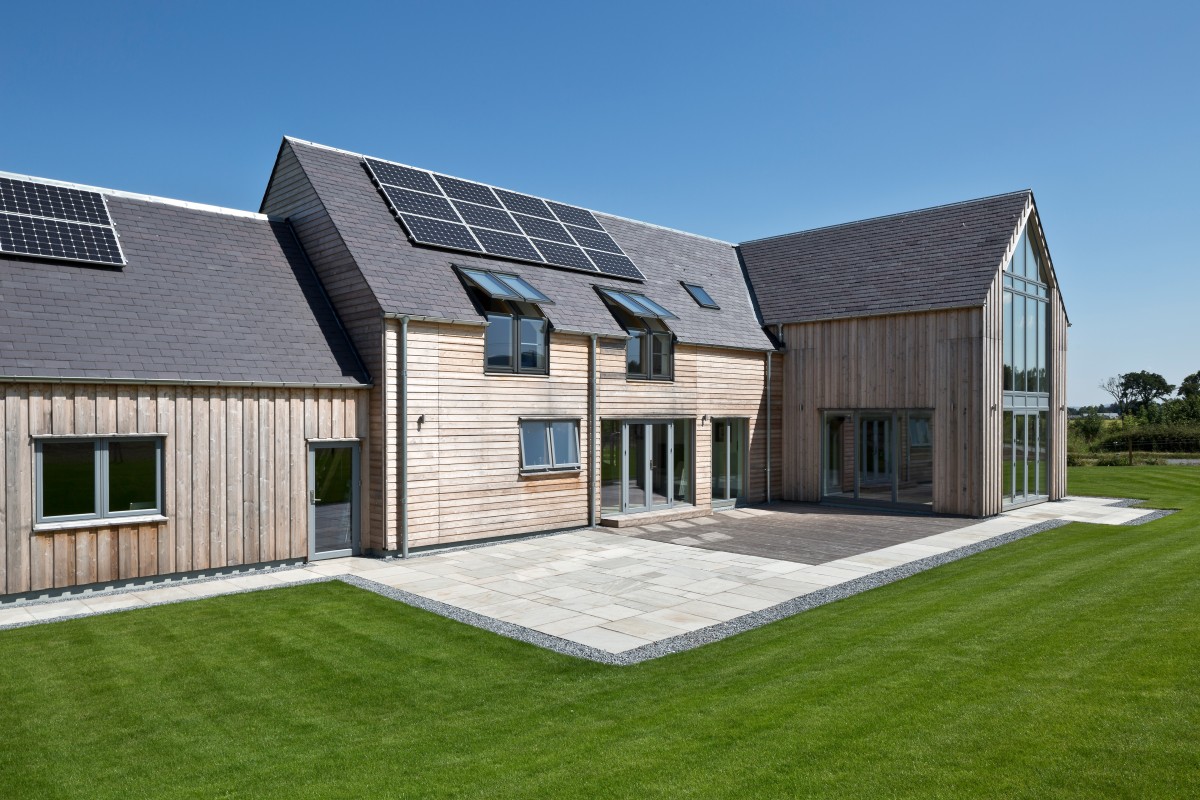
The last thing to consider when designing your home with the Fabric First approach is the heating strategy – it is achievable to get the heating demand down as low as 3 or 5 KW even in the UK. The most cost-effective way to provide the heating demand is through a small boiler and underfloor heating (on the ground floor only). There are some renewable heat incentives that you get from using air source or ground source, but the upfront purchase cost is still huge given the low heating demand required. We would suggest using the PHPP or SAP calculations to work out what the heating requirements are for your home, and then getting a heating company to design the system you require.
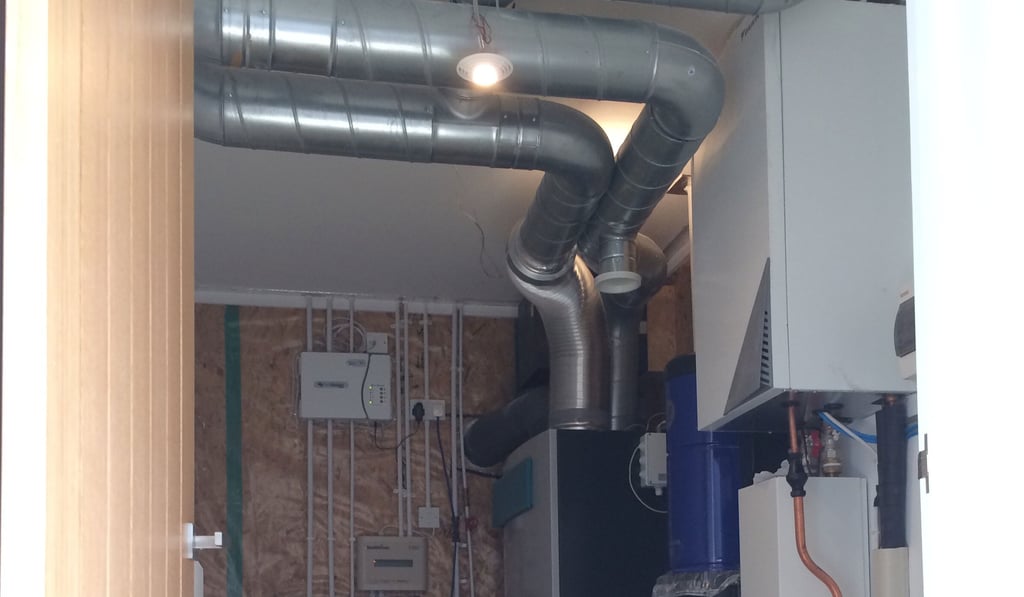
“Integrate Fabric First with everything you are going to do. Take the principles of Fabric First and use it, because it will save you a lot of money in construction process and in the long-term of the project”.
- Allan Corfield, MD and Chartered Architect
If you follow all the stages of the Fabric First approach to your self-build, you will achieve a low-energy home for a reasonable cost. And if everything is applied correctly, your effort and investments will pay back in low energy bills and the satisfaction that your home is good for the environment.
This article was inspired by the 'Beginners’ Guide to Building a Low-energy Home' series delivered at the Homebuilding and Renovating Show by Allan Corfield. If you have any questions for Allan and the team about your project, don't hesitate to get in touch.