Thanks to Iga Panczyna, our Senior Architect and certified Passive House Designer, we now offer full Passive House design and certification services. In order to give you a sense of what the Passive House (Passivhaus – as it is in German) standard is, we wrote this two-piece article presenting all the important information on this concept. The first part introduced the concept of Passive House and its fundamental features. The second one presents a more detailed description of the principles required of this building standard such as preventing heat loss and maximising solar gains. If you are considering building a passive house, this article is a perfect start.
PREVENTING HEAT LOSS
One of the most important factors in designing Passive House standard is to minimise a building’s heat loss. To achieve it, the building fabric and windows have to be designed in particular ways:
1. Building Fabric
– Super insulation – the building fabric is one of the most important factors of a successful Passive House construction. The insulation surrounding a Passive House building should be applied without gaps, creating a continuous thermal envelope around the entire heated area of the building, similar to a giant sleeping bag. These super insulated wall, roof and floor elements play a large role in reducing the amount of heat loss, making it possible to heat the building without a conventional heating system.
These components have a recommended U-value of less than 0.15 W/m²K (sub-criteria) and can vary in size with typical Passive House wall and roof constructions being up to 450-500mm thick (with typically 300mm insulation or more).
– Air-tightness – in addition to the super insulation, the building envelope is surrounded by one continuous airtight layer with all components and connections fitted in an airtight manner. Air-tightness tapes and seals are applied around all areas where components meet, with special attention paid to the installation of electrical and mechanical services. Air-tightness in a Passive House is verified by conducting a pressure test (blowerdoor test) to measure the amount of air changes the building experiences within one hour.
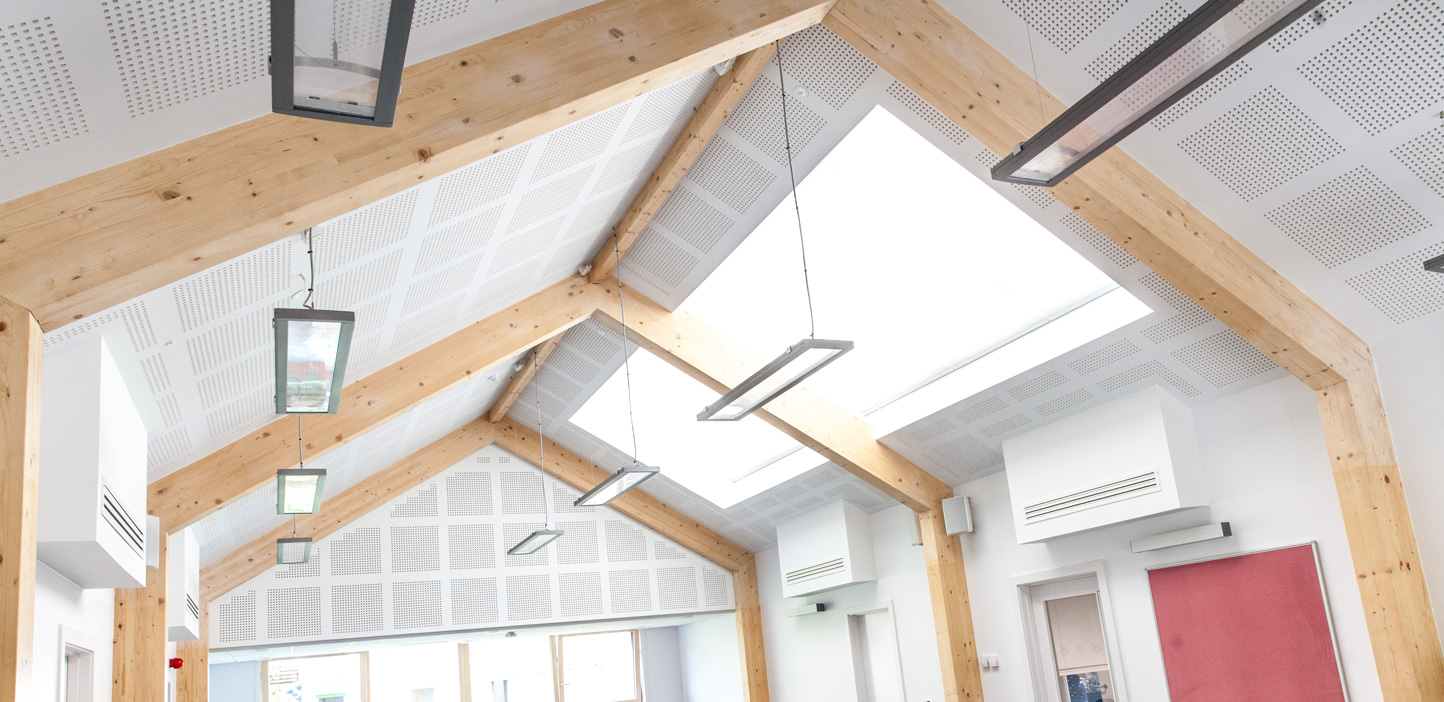
To achieve certification, the building’s pressure test result (measured at 50 Pascal difference between inside and outside) must not exceed more than 0.6 ac/h־¹. If the buildings air changes per hour are more than 0.6 ac/h־¹ then too much heat will be lost through leakages and the reduced energy targets of less than 15kWh/(m²a) will not be reachable.
– Thermal bridge free design – the third way in which heat loss can be reduced through the building fabric is to eliminate the thermal bridging effect. Windows and door frames are insulated over, and the building is detailed in such a way that areas where solid components meet are reduced, or eliminated, so that heat does not have a clear path from the inside of the building to the outside.
Thermal bridge calculations are conducted (commonly using the therm or heat programmes) in order to accurately detect and eliminate any area that may create a thermal bridge. Thermal bridging within a Passive House building is recommended to be below 0.01 W/(m²K) (sub-criteria) as calculated on an external dimensions basis.
2. PASSIVE HOUSE WINDOWS AND DOORS
The windows in a Passive House are required to have a much lower U-value than standard windows so as to prevent excessive heat loss. The recommended Passive House window U-value is no higher than 0.8 W/(m²K) (sub-criteria) and an installed U-value of no higher than 0.85 W/(m²K) (sub-criteria). These values are achieved by a combination of triple glazing with two low-e coatings (typically on glazing surfaces 2 & 5 and filled with argon or krypton gas), warm edge spacers and frames with increased insulation levels (sub-criteria).
Whilst this reduces heat loss through the windows, this element of the Passive House building has a dual purpose and must also allow a beneficial amount of solar gains to enter the dwelling. With this in mind the window glazing must have a minimum solar energy transmittance factor of 50% (G-factor = 0.5, sub-criteria) with 62% (G-factor 0.62) being the highest currently achievable with Passive House windows.
The human body is particularly sensitive to temperature differences within a room, in the form of radiant temperature asymmetry and temperature stratification. Radiant temperature asymmetry describes a situation where objects simultaneously radiate different temperatures towards our bodies, in this situation a temperature difference of 4K or above will cause discomfort. Temperature stratification describes a situation where there is a temperature difference between heights of 1.1 to 0.1m within a room, in this case a temperature difference of 2K or above is enough to cause the feeling of discomfort.
An advantage of such low heat loss values through the Passive House window components is that their internal surface temperatures will be higher than 17°C (sub-criteria), even during the evenings in winter. The result of this is a dramatic improvement in a buildings thermal comfort. Especially when sitting next to the windows, as the improved internal temperature will eliminate cold drafts due to temperature stratification and discomfort due to a radiant temperature asymmetry within a room. For more information about triple glazing read our article here.
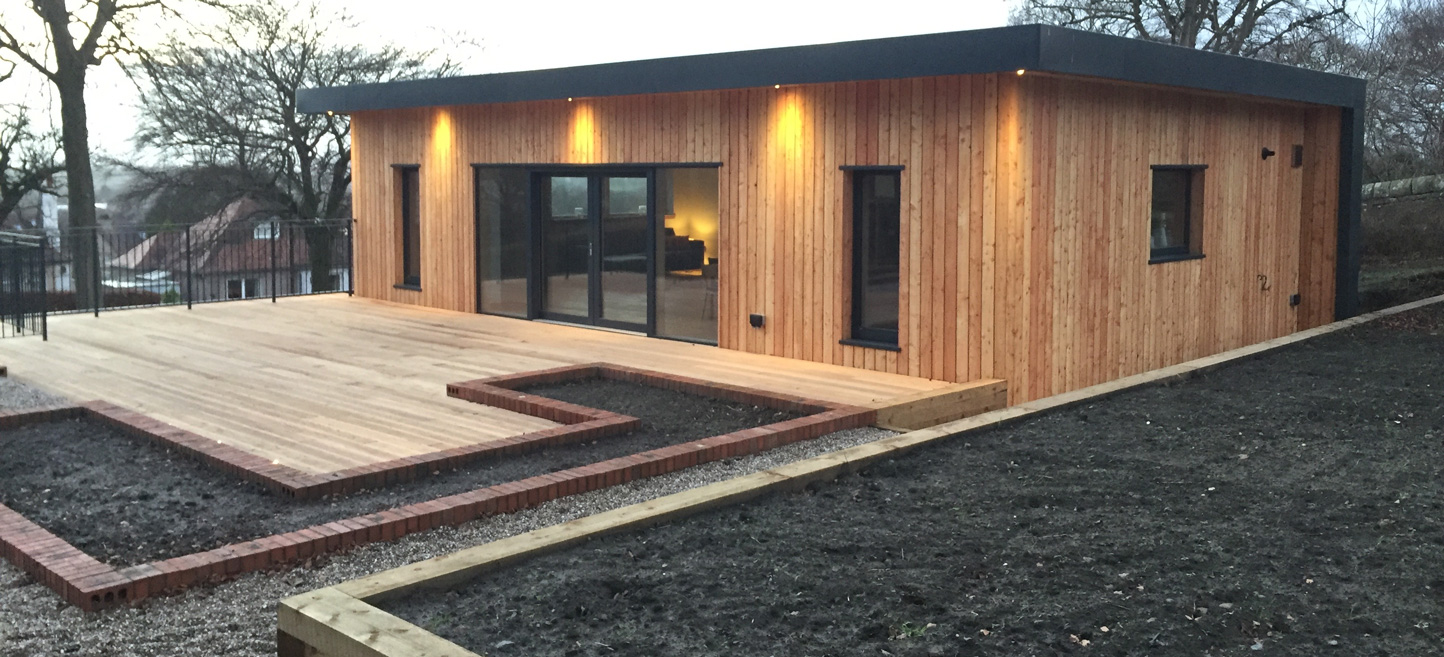
Doors are also a crucial component of the Passive House construction. They feature high insulation values and are designed for airtightness to prevent heat loss and drafts. Quality hardware, locks, and proper installation are essential for performance and security. Door orientation and shading are carefully considered for optimal energy gain and heat control. Material selection, including wood, uPVC, or composites, is vital, and doors must meet security and safety requirements while adhering to Passive House standards.
MAXIMISING HEAT GAINS
Another crucial factor in designing a Passive House is to maximise heat gains a building can achieve. Amongst the solution that help you with this are MVHR, space heating, lighting and other appliances.
1. Mechanical Ventilation with Heat Recovery (MVHR)
All of the rooms within the thermal envelope (inside the continuous air-tight layer) are ventilated via the use of a mechanical ventilation system with heat recovery. The requirement for performance of an MVHR system, within a Passive House, is a minimum heat recovery efficiency of 75%, with an energy consumption of no more than 45Wh/(m³) (sub-criteria).
The ventilation system provides a steady stream of fresh warm air to the building which is an absolutely vital requirement as the building envelope renders the building almost completely airtight. The average air change rate per person in a Passive House is 20-30 m³ h־¹ (sub-criteria) with higher air change rates in rooms with excess moisture, or odours such as kitchens and bathrooms.
The air flow rate of the ventilation system must be balanced which is most commonly achieved by dividing the house into supply air rooms (such as bedrooms and living/dinning rooms) where fresh air is provided; overflow areas (such as hallways and stairwells/landings) where the air is drawn across a space; and exhaust air rooms (such as kitchen, bathrooms and laundry rooms) where the stale air leaves the building.
The heat recovery part of the ventilation system recycles the heat from the used stale air and uses this to pre-heat the fresh clean air being pumped in to the building (with a minimum efficiency of 75%). This means that in order to reach the Passive House internal design temperature of 20ºC (sub-criteria) the building only requires an additional 4-5˚C from space heating, as the other 15-16˚C will be recovered from the exhaust air, and channelled back into the building through the supply air. For more information about MVHR systems read our article here.
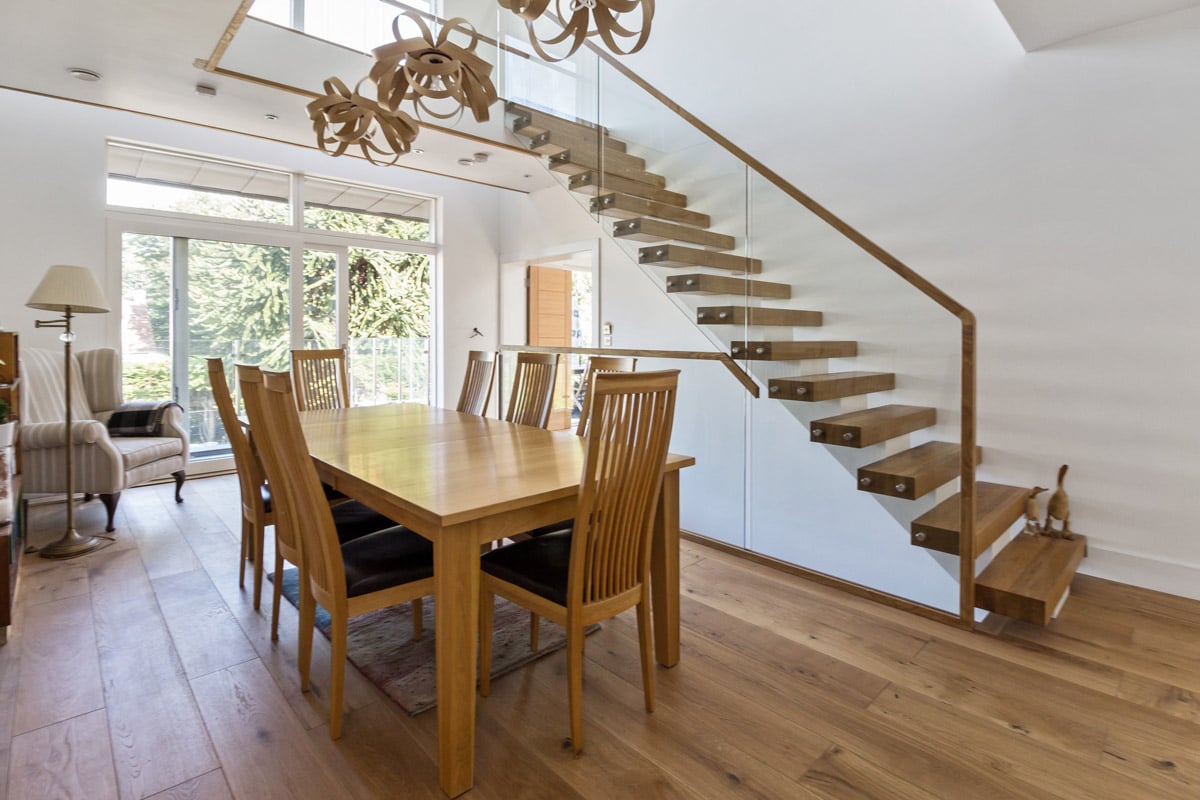
2. Space Heating
An efficient MVHR system ensures that the buildings space heating requirements are reduced to such a degree that conventional heating systems are no longer required. In addition to the 15-16˚C the building receives from the MVHR unit, solar gains obtained from the large south facing glazing and internal heat gains, such as body heat, (an average person can emit 100W of heat energy) lighting and household appliances will easily provide the remaining 4-5˚C required to achieve the design temperature of 20˚C.
In some months (mainly summer and autumn) the house will reach this temperature very quickly and must rely on external shading and shock ventilation to prevent the house from over heating by more than 10% (sub-criteria) at which point it would become very uncomfortable. A useful technique for avoiding overheating in the summer is a summer bypass function within the MVHR unit. This allows the system to prevent the heat recovery function therefore reducing the amount of heat that is brought into the building without reducing the amount of fresh air.
This source of heat can take the form of electrical heating coils, a small heat pump, solar thermal or even the more conventional oil burner or natural gas. For the purposes of reducing smells from singed dust that may be in the ducts, despite the numerous filters, the supply air temperature must not exceed 52˚C.
3. Lighting and Appliances
Low energy lighting and efficient household appliances are most commonly used within Passive Houses in order to achieve the primary energy consumption criteria of less than 120 kWh/(m²a).
These appliances are carefully selected for their low energy requirements and high performance standards. LED lighting is commonly employed for its energy efficiency and long lifespan. This emphasis on energy-efficient appliances and lighting not only aligns with the sustainability goals of Passive House but also contributes to lower utility bills for occupants. Additionally, it fosters a more eco-conscious lifestyle, promoting a greener and more sustainable future.
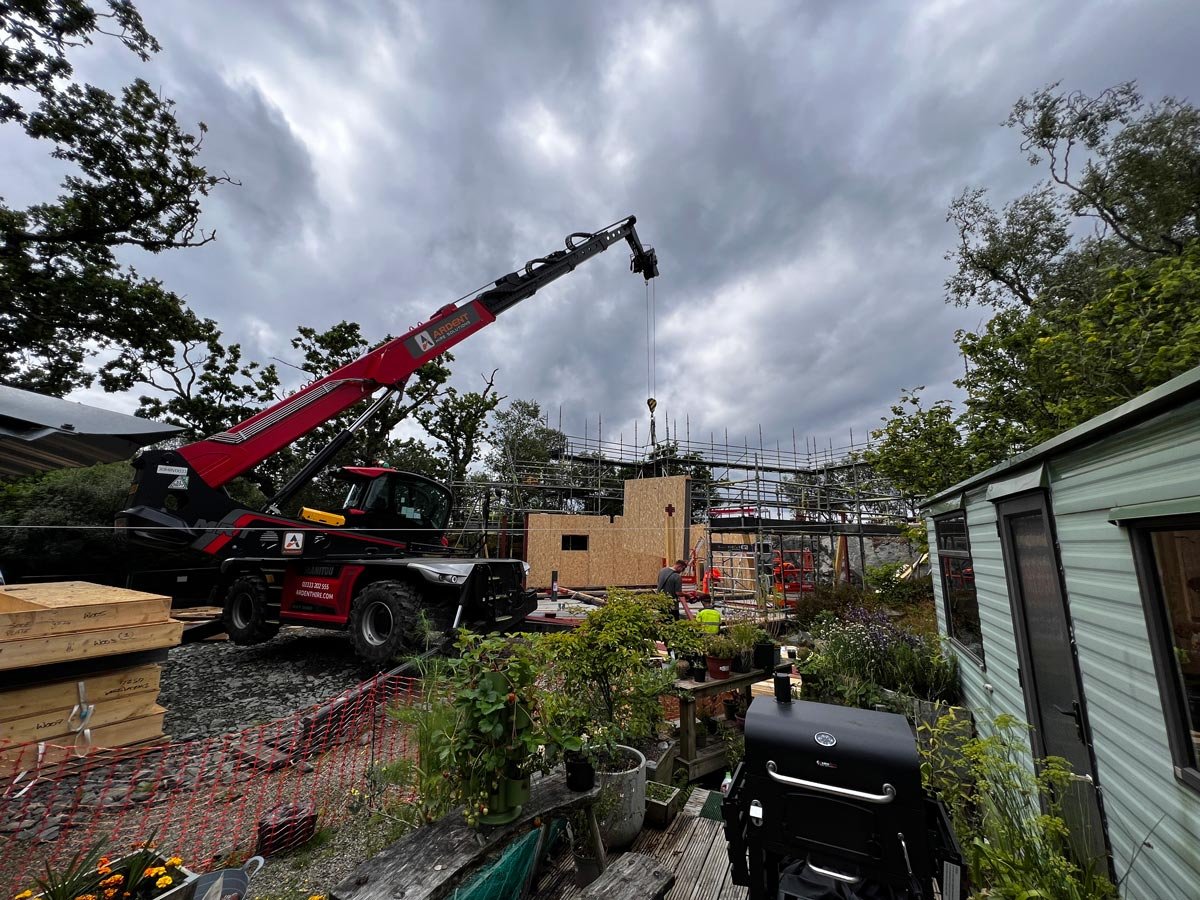
CONTINUOUS MONITORING AND PERFORMANCE VERIFICATION
In Passive House construction, continuous monitoring and verification play a pivotal role in maintaining the standard’s rigorous energy efficiency criteria. This involves the use of sensors and systems to track the building’s performance over time. Any deviations from the Passive House standards can be promptly identified and addressed by continuously monitoring factors like temperature, humidity, and energy usage.
This proactive approach ensures that the building consistently operates at peak energy efficiency, providing its occupants with optimal comfort and air quality while minimising energy consumption. Ultimately, monitoring and verification reinforce the Passive House commitment to sustainable and eco-friendly building practices.
ADAPTATION TO LOCAL CLIMATE
Passive House design is highly adaptable to local climate conditions, aiming to optimise energy performance based on geographic location. In colder northern climates, emphasis is placed on robust insulation, airtightness, and maximising solar heat gains to minimise heating demands during cold winters. Conversely, in temperate southern climates, the focus may shift towards effective shading and natural ventilation strategies to combat heat gain during hot summers.
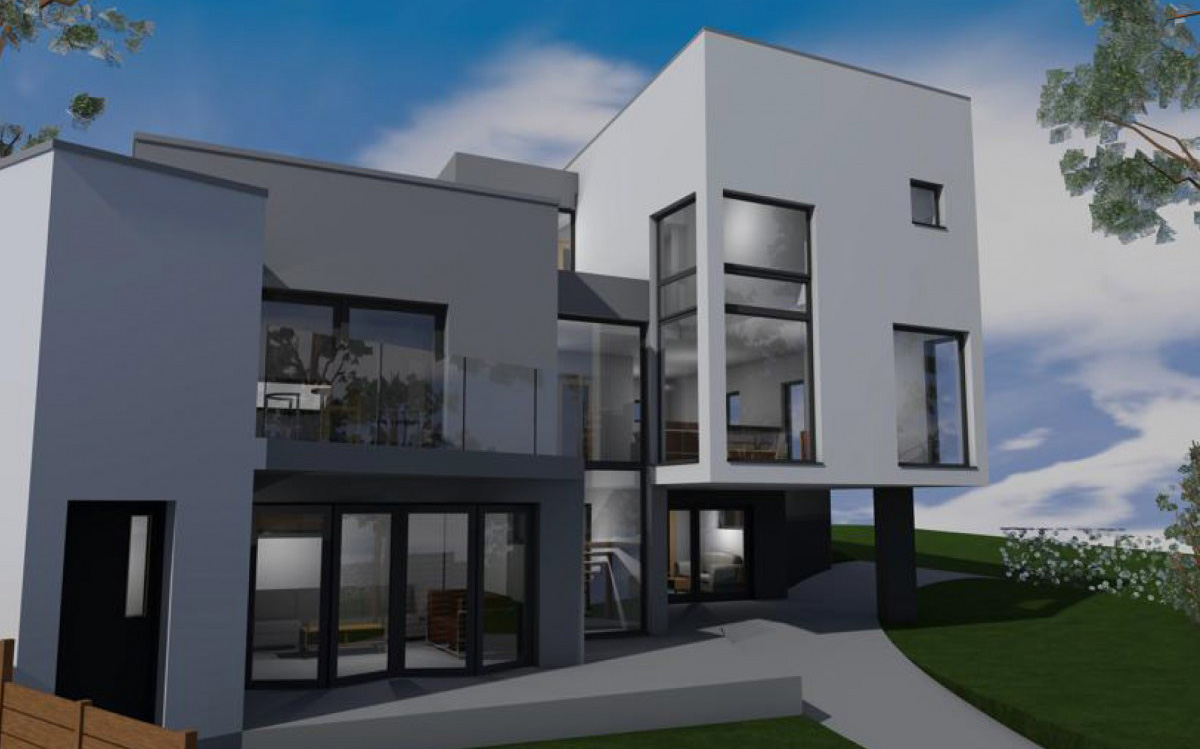
TO CONCLUDE
Clearly, interest levels in Passive House are high. The Passive House Standard’s potential to provide the UK with a solution to the problem of excessive energy consumption and high carbon dioxide emissions is now being recognised. The Passive House standard is founded on a set of simple and well established planning and construction methods, none off which are difficult to understand or implement.
However, the key to correct implementation will be in the training and knowledge available to the professionals and tradesmen employed to apply the Standard. Unlike normal building projects it is imperative that when building a Passive House each person involved understands the impact mistakes can have on the overall goal the team is striving to reach.
We are now in the fortunate position of being able to learn from the lessons and mistakes experienced in Germany and Austria during their over 20-year development of the Passive House Standard. These experiences should be used to assist and guide us towards a Passive House model ideally suited to the British climate that will provide us with a benchmark to work from, in the struggle towards a greener and more sustainable, low energy future. In doing so, Passive House design could not only help us reach our ambitious targets for 2020 and beyond, but it could, in fact, be responsible for us achieving those targets.
If you would like to read more about Passive House Standard, read the article with our guest Ben Adam-Smith, an eco home enthusiast, and House Planning Help founder, website dedicated to inspiring a new breed of self-builders to build energy efficient homes. In his article, he presents the reasons why he decided to build a passive house, real examples of completed houses and top tips on how to achieve this standard for your own project.
This was the second part of our ‘Introduction to Passive House Standard’ article. You can read the first one here.