We will be sharing stand 126 with SIPs Industries, and will be on hand to talk you through designing a house utilising Structural Insulated Panels (SIPs) – something we have great experience in. If you are looking for a more energy efficient construction system, using SIPs could be just the system for you.
Are you considering alternative low energy building systems? Find out your options by following the links below:
Used in the USA over the past 50 years, SIPs are now enticing a stronger interest over here in the UK. Covering all building types, from schools to retail developments, Structural Insulated Panels are also gaining popularity from the Self Build sector for their versatility. Here’s a short introduction to SIPs, so you’ll have the basics covered if you plan on visiting the Homebuilding and Renovating Show…
Made in advance before reaching the construction site, the Structural Insulated Panels (SIPs) are factory-made to the precise measurements of the building’s design. The panels are built as a composite through layering a rigid insulating material between outer boards. The subsequent panel is strong whilst also very well insulated. In addition to this, the SIPs are extremely lightweight and quick to erect – due to their precise digital design. The most common materials in SIPs manufacturing are Oriented Strand Board (OSB) with a core of Expanded Polystyrene (EPS), although a range of other materials can also be used.
Depending on design, the Structural Insulated Panels are available in a choice of thicknesses, and can be used for walls, floors and roofs for all types of buildings. The large prefabricated units (1.2m wide x 4.8m long) can be installed on site quickly, saving labour costs and allowing the work from subsequent tradesmen to begin earlier. SIPs also offer many other timesaving benefits, including pre-cut (or pre-fitted) door or window openings. Openings can be cut on site, however, it is important that this is agreed in advance with the SIPs provider, and that they are a minimum of 500mm from the top of the panel. Utilising SIPs over traditional timber frame can save on average 4 weeks site time and almost 8 weeks for a traditional brick built home.
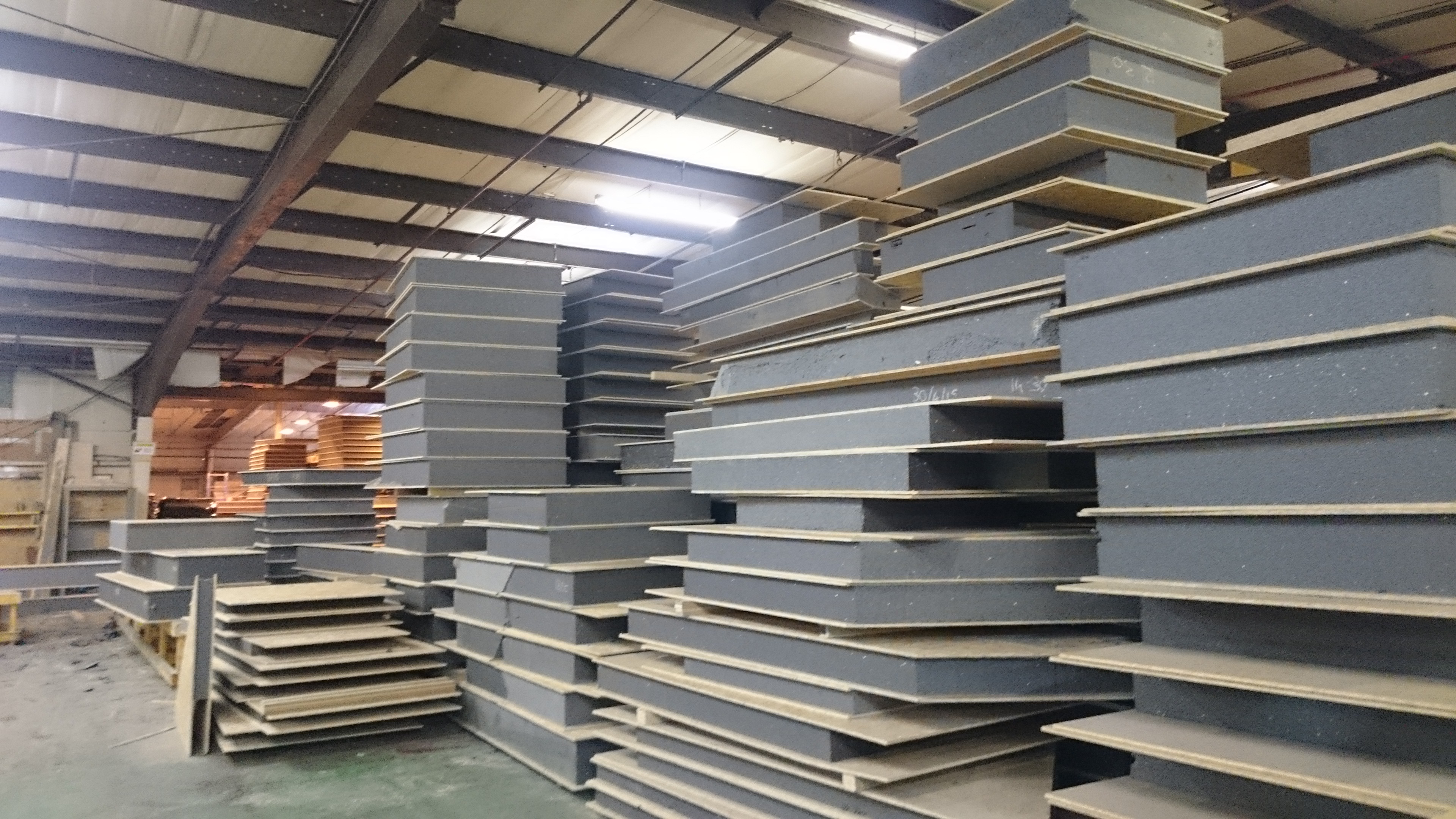
For designs integrating SIPs into walls, floors and roofs, a degree of uniformity can be achieved at the building’s interfaces – meaning less air leakage and greater consistency with the construction’s overall insulation. SIPs have become a popular method of construction due to these environmentally friendly properties. Creating airtight structures is paramount to reducing energy bills and SIPs are excellent at this.
As the panels are factory cut, the accuracy and fitting of the panels is much better than in traditional construction methods. Another key aspect of energy efficient homes is the reduction of repeated cold-bridging, needed when striving for Passive Haus Certification. As the panels are larger than in timber frame construction, the spacing of structural timbers goes from 600mm centres to 1200mm centres – this dramatically reduces the amount of timber battens (thus giving more insulation).
Local authority planners tend to insist that new housing should meet higher levels of the Code for Sustainable Homes, and so SIPs is a welcomed building system. Improving the U-Values of walls and roofs can be fairly straightforward simply by increasing the levels of insulation, there are therefore a number of commonly used panel widths.
Ranging from 117mm (internal load bearing walls), 167mm, 217mm and over 300mm for Passive Haus projects. The very precise, engineered process delivers excellent efficiencies, and as each and every panel is cut to the correct size beforehand, there is minimal onsite waste. Any of the timber off-cuts in the factory can usually be fully recycled too.
SIPs also offer a lot aesthetically as a design concept, as they can be used to create open or vaulted roof spaces. Typically, roof construction relies on a conventional trussed roof to develop the roof space, but as SIPs are glued together following a precise design, they can span from ridge to eaves (max 4.8m) with, at most, one intervening horizontal beam. Building roofs with SIPs is therefore a much quicker process compared to other conventional roof systems, and is very cost-effective as the insulation is built in. For this reason, SIPs are proving very popular with room-in-the-roof designs – and are particularly useful for building one-and-a-half storey houses, and three storey townhouses.
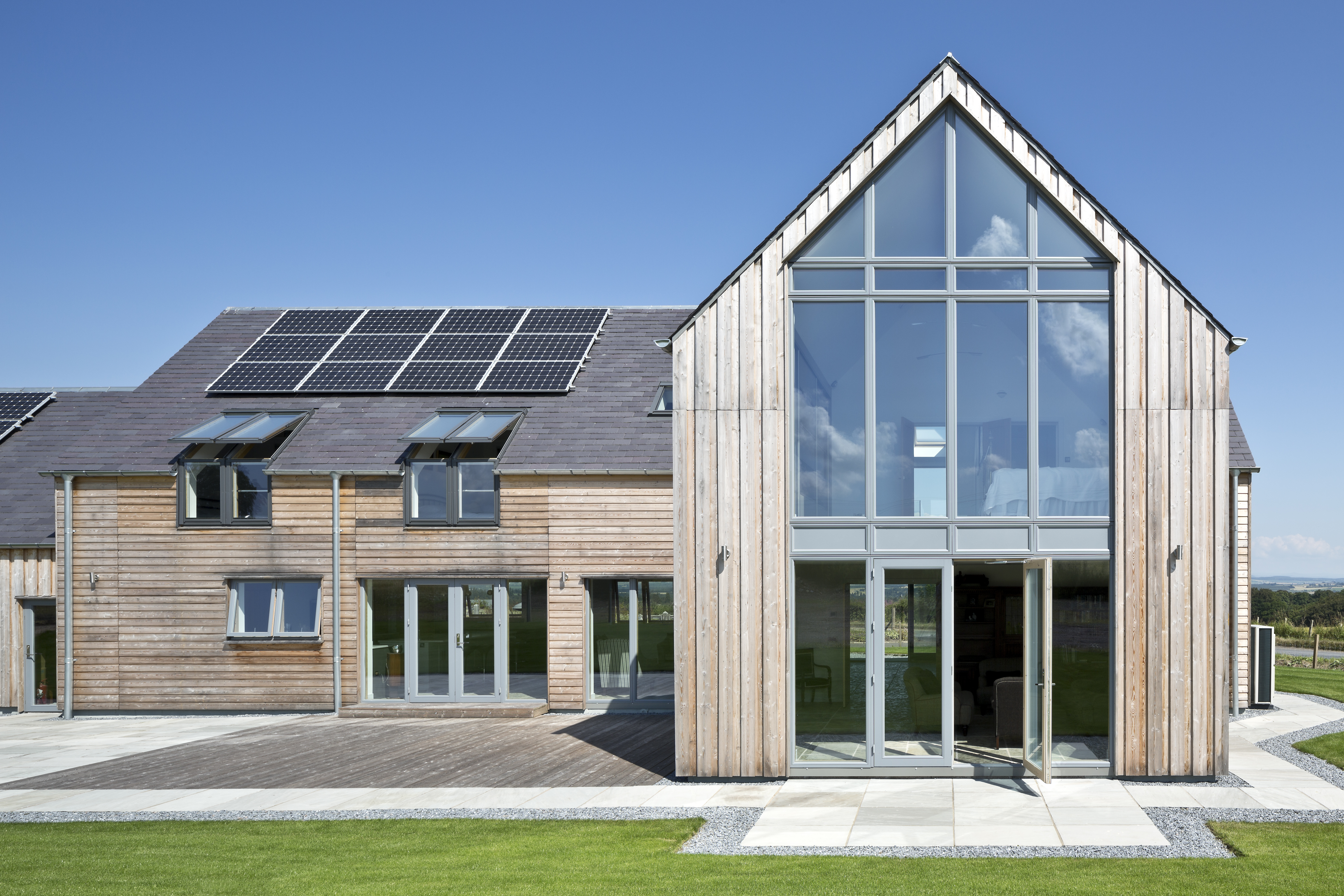
For some Self Builders, SIPs have become popular as a wrap-around for homes being built with a traditional oak frame. Using the Structural Insulated Panels as an infill means a great balance between style and practicality can be achieved – for example, your home can be kept well insulated by the SIPs, but it can also display charm and character by leaving the timber framework exposed.
Due to the frame providing both the structure and the insulation, you gain a huge amount of flexibility on the buildup of the external leaf. Traditionally when finishing a building in render you need to build a block-work wall to render onto, which has to sit on a foundation and be tied to the kit. However with a SIPs kit you can utilise lightweight render carrier boards which can be fixed directly to the kit via timber battens. This removes the need for block-work and the foundation which it sits on.
The cost involved in utilising a SIPs construction method tends to be between 5-10% more than the likes of Timber Frame, or Brick and Block, however, this 10-15% more on the frame price actually represents around 3-5% of the overall project costs. This is a result of the savings made through the built-in insulation, as well as the enormous amount of on-site time saved by choosing SIPs. Having a SIPs-built home also brings lower energy costs over the life of the property. The majority of SIPs homebuilders tend to install a mechanical ventilation heat recovery system, in order to make the most of the incredibly high levels of airtightness. This maintains comfortable internal temperatures, and recycles the building’s heat very efficiently.
So, in opting for the Structural Insulated Panels (SIPs) construction method, you can save costly on-site time, as well as energy costs in the future. With a reliable reputation for airtight and comfortable living spaces, SIPs might be the building system for your Self Build project.
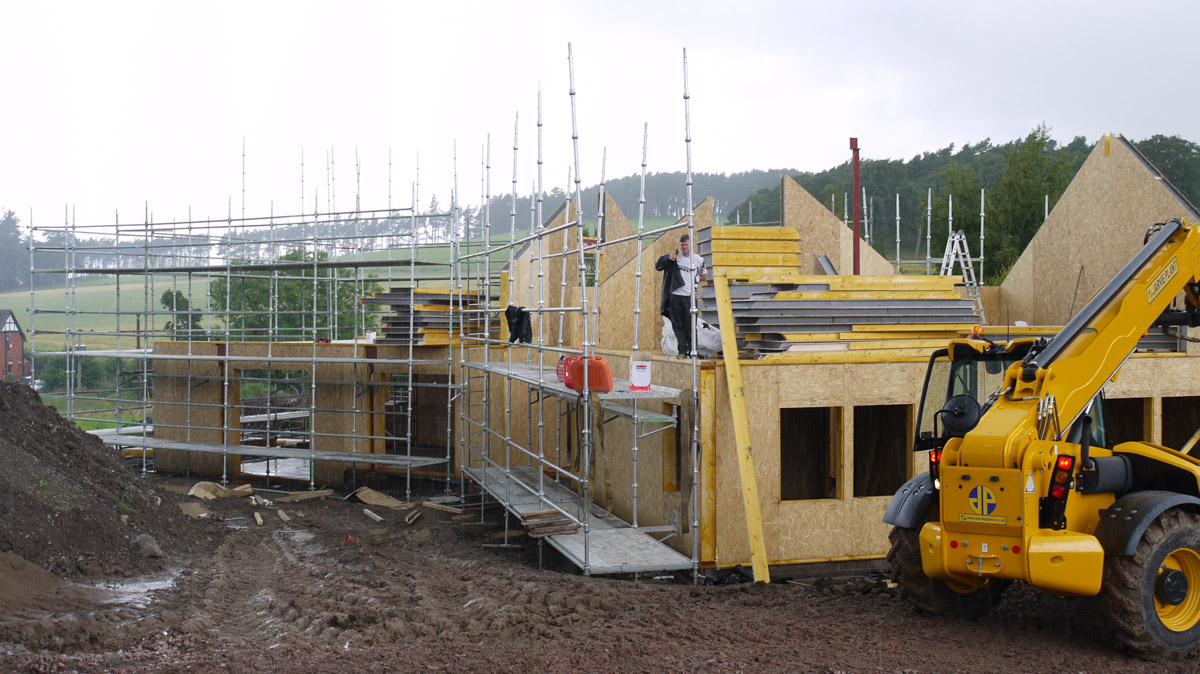
As mentioned, Allan Corfield Architects specialise in the design of Structural Insulated Panels homes – so do not hesitate to contact us if you would like to discuss your SIPs project in more depth! ACA are a member of the Structural Timber Association (STA), which provides advice and training on timber based construction.
Are you considering alternative low energy building systems? Find out your options by following the links below:
We would be more than happy to chat to you if you’re heading to the Homebuilding and Renovating Show in Edinburgh, 24th and 25th October 2015. Allan will be a guest speaker on the Saturday afternoon, offering a client case study – talking visitors through Colin Amor’s Barn-Style SIPs Eco Home which was completed in 2014. Don’t miss out!