We are facing housing challenges in the UK. There’s an alarming shortage of quality homes, and even when new homes are being built, they often fall short of the standards we hope to see. While building regulations are gradually improving, many of us believe it’s still not going far enough.
Our vision is clear – we no longer want to settle for EPC ratings of C on our new homes in the UK. We aspire to reach A or even better. We need homes that not only reduce heating costs but also create a comfortable environment without overheating issues. So, as we embark on this journey, we’ll uncover the tools and techniques to build low-energy homes that meet and exceed these aspirations right here in the UK.
FABRIC FIRST APPROACH
Every architect strives to design aesthetically pleasing homes, but we believe that good design must go beyond aesthetics. It must be rooted in a deep understanding of the building’s surroundings. For those of you considering the exciting path of Self Building, the Fabric First approach encourages you to start by considering the site’s unique features, orientation, and natural resources.
Our goal is to harness the power of these natural elements, making the most of solar gain while minimising heat loss. But how do we achieve this balance? It all begins with thoughtful layout choices within your chosen construction method. Whether your site boasts remarkable landscapes or faces unique climate challenges, the choice of construction method can make a significant difference.
As you progress in your home-building journey, you’ll naturally explore the finer aspects of construction. This involves addressing important factors like airtightness, preventing cold bridging, and ensuring these elements align with your low-energy goals. We understand that every homeowner’s goals are unique, and not everyone seeks to achieve a Passive House certification. Some may desire a beautifully designed, environmentally conscious home that still aligns with their vision. When you reach those goals, the focus naturally shifts toward ventilation strategies and heating systems.
For many of us, this leads to considering Mechanical Ventilation with Heat Recovery (MVHR) systems for optimal ventilation and low-energy heating solutions.
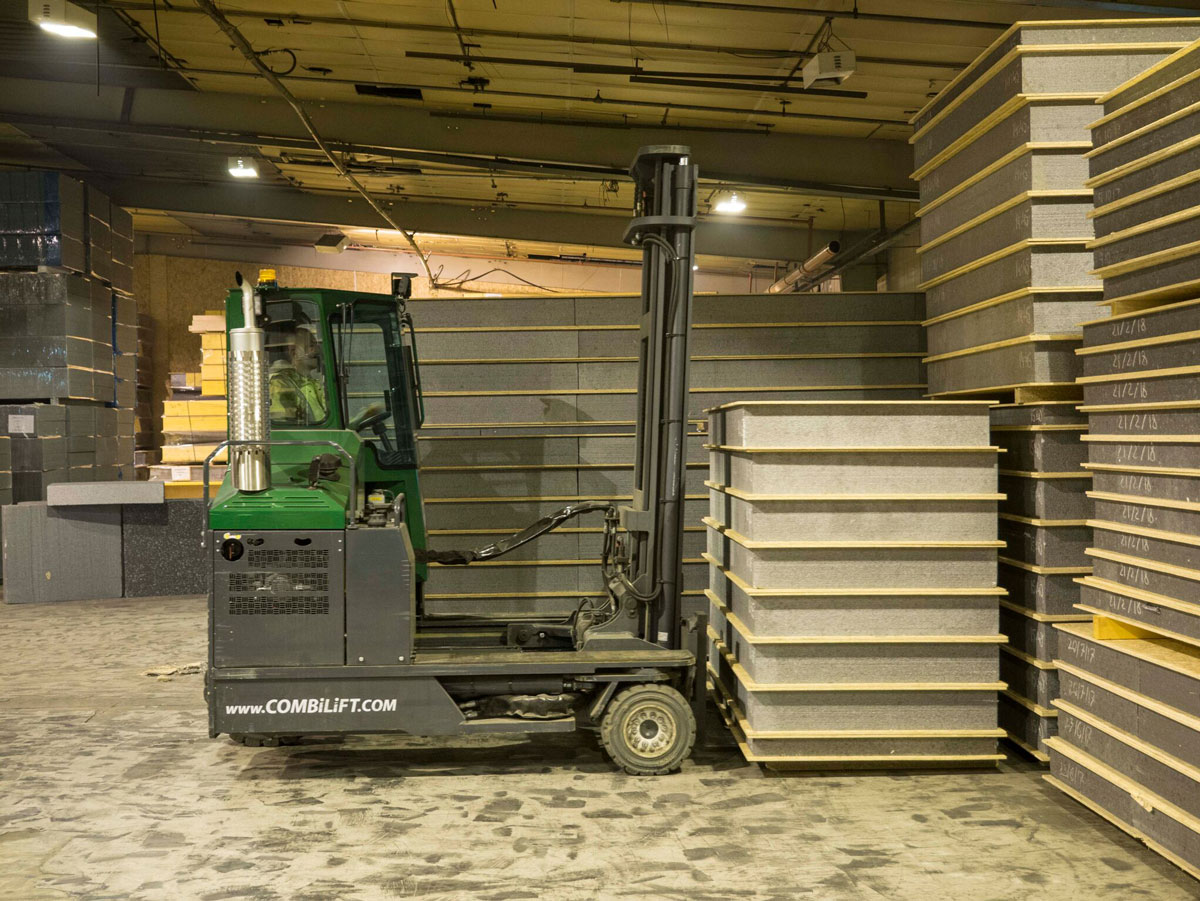
STRUCTURAL INSULATED PANELS AS A SOLUTION FOR YOUR LOW ENERGY HOME
Structural Insulated Panels, commonly referred to as SIPs, stand out as a modern and efficient construction method known for their outstanding performance in achieving low-energy homes. At Allan Corfield Architects, we have extensive experience with SIPs construction and have witnessed its numerous benefits.
So, what exactly are SIPs? They can be described as sandwich panels. These panels consist of two layers of Oriented Strand Board (OSB), which are filled with rigid insulation in between. The result is a robust structural panel that offers excellent thermal properties while maintaining structural integrity. SIPs are characterised by limited timber content within the panel, which significantly reduces the risk of cold bridging.
What sets SIPs apart is their versatility. The roof and wall panels are identical, simplifying construction and reducing potential errors. While SIPs currently represent a smaller market share in the construction industry, they are steadily gaining ground. Traditional building methods, especially in England, still dominate, but innovative approaches like timber frame, SIPs, and Insulated Concrete Formwork (ICF) are on the rise.
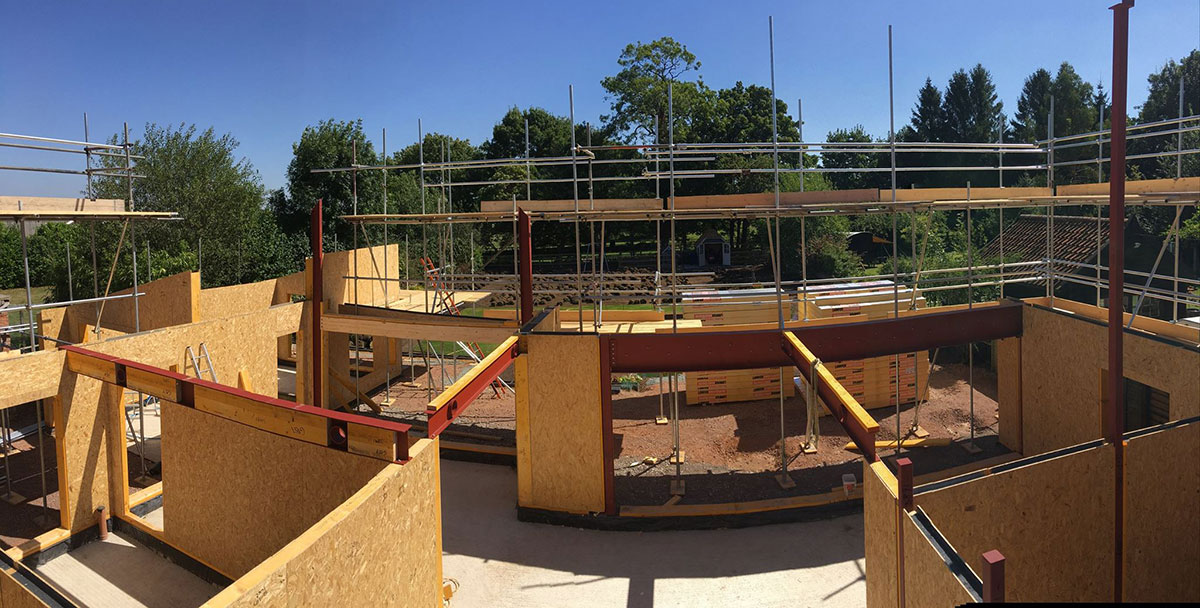
One compelling reason to opt for SIPs is their efficiency and speed of construction. These panels are prefabricated to your exact design specifications in a factory, reducing on-site construction time. They are shipped in panels that seamlessly fit together like a jigsaw puzzle, resulting in a swift build time of approximately six weeks.
Though SIPs may come with a slightly higher price tag (typically 10% to 15% more expensive for the envelope component), their precision and rapid construction process offset the costs. The accuracy of SIPs construction allows you to order windows and doors at the same time as your kit, knowing they will fit perfectly when they arrive on-site.
One of the standout features of SIPs is their ability to create expansive, uninterrupted spaces. With SIPs, you can achieve vaulted ceilings with a single ridge beam at the centre, creating a spacious, open interior. This design flexibility is particularly appealing to those who desire the aesthetic of a vaulted ceiling without any visible structural support.
In terms of concerns about insurance and mortgage approval, SIPs pose no issues. Both insurers and mortgage providers understand and accept this construction method. They primarily consider the external finishes for fire protection and take into account the inherent fire resistance provided by plasterboard on the interior.
Low-energy home designers, like us at Allan Corfield Architects, have a strong affinity for Structural Insulated Panels (SIPs) due to several compelling reasons. These panels offer numerous benefits that align perfectly with our mission of creating energy-efficient, sustainable homes.
Another standout feature of SIPs is their exceptional thermal efficiency. SIPs boast a high insulation value thanks to their limited timber content. This inherent insulation property dramatically reduces the chances of heat loss and cold bridging within the construction. As a result, achieving compliance with building regulations and Standard Assessment Procedure (SAP) calculations becomes a smoother process. SIPs often come with PSI values, which can be seamlessly integrated into SAP calculations, providing an accurate measure of how the product and construction method perform.
In addition to thermal efficiency, SIPs also contribute to consistent indoor temperatures. This stability is particularly noticeable when coupled with Mechanical Ventilation with Heat Recovery (MVHR) systems, which help balance and distribute heat efficiently due to the high airtightness of SIPs.
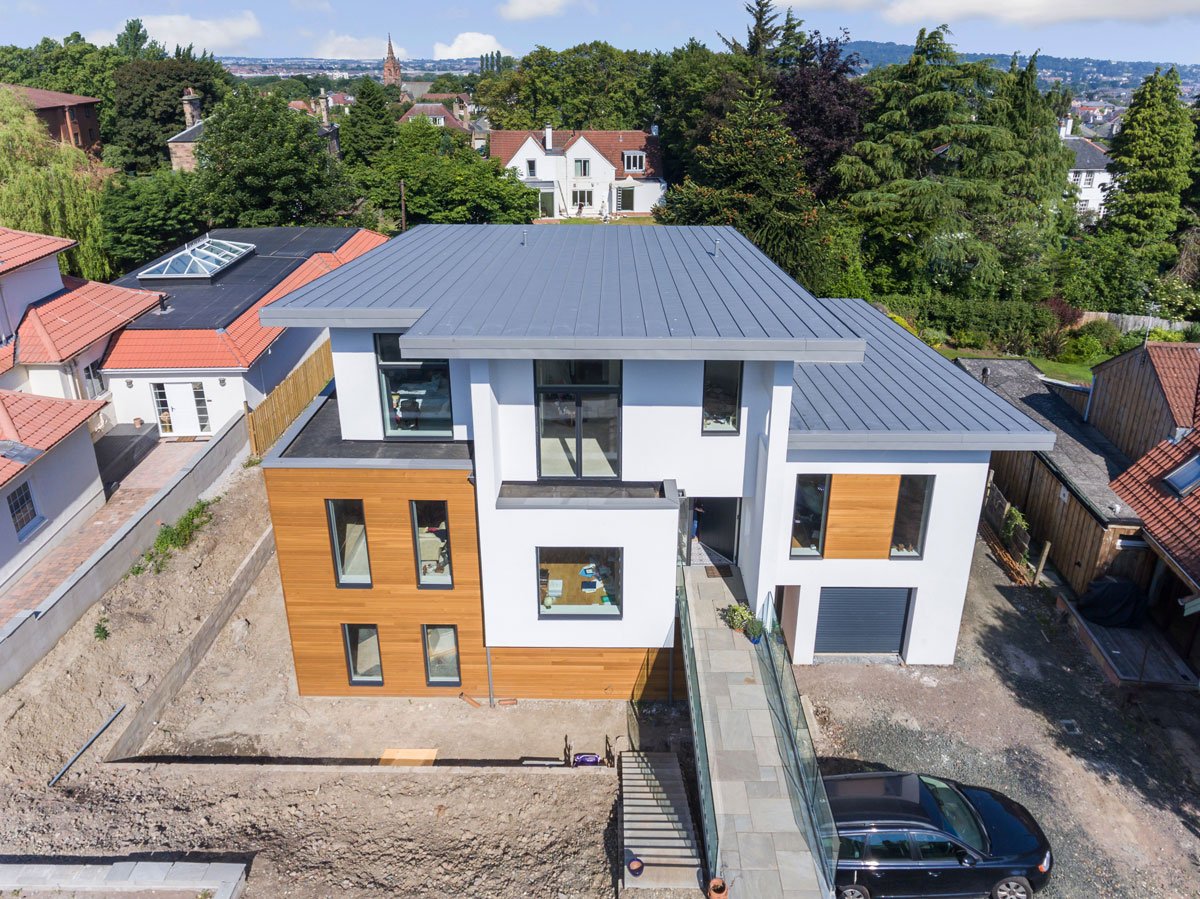
SIPs construction minimises drafts and eliminates the presence of cold spots commonly found in older homes with deteriorating insulation. The rigid insulation within SIPs remains in place, ensuring a reliable and consistent thermal barrier. The airtight envelope created by SIPs construction prevents heat loss and maintains comfortable indoor conditions.
Airtightness is a critical aspect of SIPs that designers value highly. The panels’ male-female joint design, coupled with airtightness tape, results in a remarkably sealed construction. Achieving high levels of airtightness is a goal we often recommend, even if a Passivehaus design is not the target. The tighter the construction, the better the overall performance, minimising cold drafts and ensuring moisture control.
SIPs also offer excellent sound insulation, making them an ideal choice for homes located near busy roads or for those seeking a quieter living environment. This level of acoustic comfort enhances the overall quality of life within the home.
Moreover, SIPs easily meet building regulations’ requirements for airtightness, simplifying the compliance process. These features make SIPs a preferred choice for low-energy home designers, as they align seamlessly with our goals of creating energy-efficient, comfortable, and sustainable living spaces.
DESIGN ATTRIBUTES OF SIPS
When considering the design attributes of Structural Insulated Panels (SIPs), it becomes evident why architects and homeowners alike are drawn to this construction method. SIPs bring an array of design possibilities and performance advantages that align with the goals of creating efficient, comfortable, and aesthetically pleasing homes.
Open and Spacious Interiors: SIPs are synonymous with creating open and spacious interiors. Their ability to form an exceptional building envelope is enhanced by the possibility of vaulted ceiling spaces. These ceilings offer a captivating two-storey height, accentuated by beams running across the centre. The result is a visually striking interior with unobstructed views of the sky. Moreover, SIPs provide versatility in panel sizes and can accommodate complex shapes, and they even allow for curved designs since the roof and walls are seamlessly integrated.
Energy-Efficient Roof Designs: SIPs extend their energy efficiency to roof designs. By using thicker panels, they enhance the insulation value of the roof, akin to wearing a warm woolly cap to stay snug. This principle ensures that the roof, like a well-insulated head, remains the warmest part of the house.
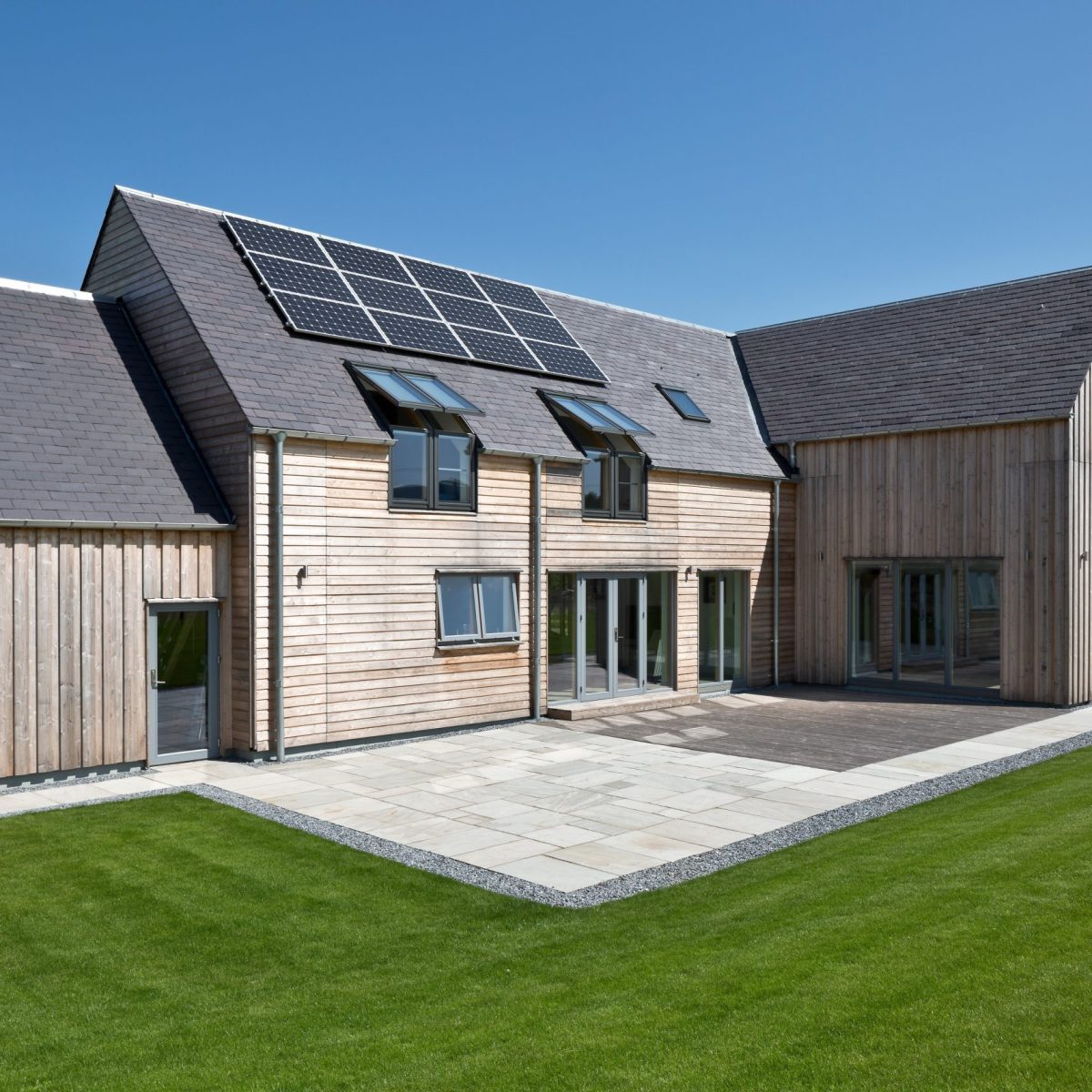
Structural Stability: SIPs are celebrated for their inherent structural stability. As rigid panels, they possess natural structural integrity. This quality makes them suitable for multi-storey buildings and cantilevered structures. The construction efficiency and precision of SIPs become evident when prefabricated off-site, leading to faster and more efficient on-site assembly. For contractors and subcontractors, SIPs offer a streamlined process, simplifying project management and reducing risks.
Design Brief: When embarking on your journey to build an energy-efficient home, these are the aspects you should discuss with your design team. Your architects should be well-versed in incorporating SIPs into your project and delivering the features and benefits they offer. By addressing these design attributes, you can ensure that your chosen professionals have the experience and expertise to guide you effectively, aligning your vision with a structurally sound, energy-efficient, and beautiful home.
INITIAL DESIGN AND PLANNING STAGES WITH SIPS
The initial design and planning stages of your low-energy home project are where the foundation for a successful build is laid. It’s here that you delve into the specifics of your site and project brief, encompassing essential factors like your budget and low-energy goals. These early decisions are pivotal, as they will shape the trajectory of your entire project.
Your design must be a response not only to your project brief but also to your site’s unique characteristics. Factors such as prevailing winds, solar paths, and your lifestyle preferences play a crucial role. Are you a fan of the morning sun in your bedroom and envision a lot of afternoon garden gatherings? This information helps maximise the functionality and benefits of your design. Additionally, understanding your site’s orientation can influence the placement of utility spaces, like a plant room.
If you’re considering Passive House certification, your design needs to focus more on elements like window placement and overhangs, ensuring their alignment with Passive House principles. Keep in mind that pursuing full certification can be more complex and costly, especially with larger and more intricate building forms, which entail more junctions and potential thermal bridges. The form factor is an essential aspect of Passive House design, with simpler box-like structures being a more straightforward path to certification. However, it might not always be the best fit for your vision or site.
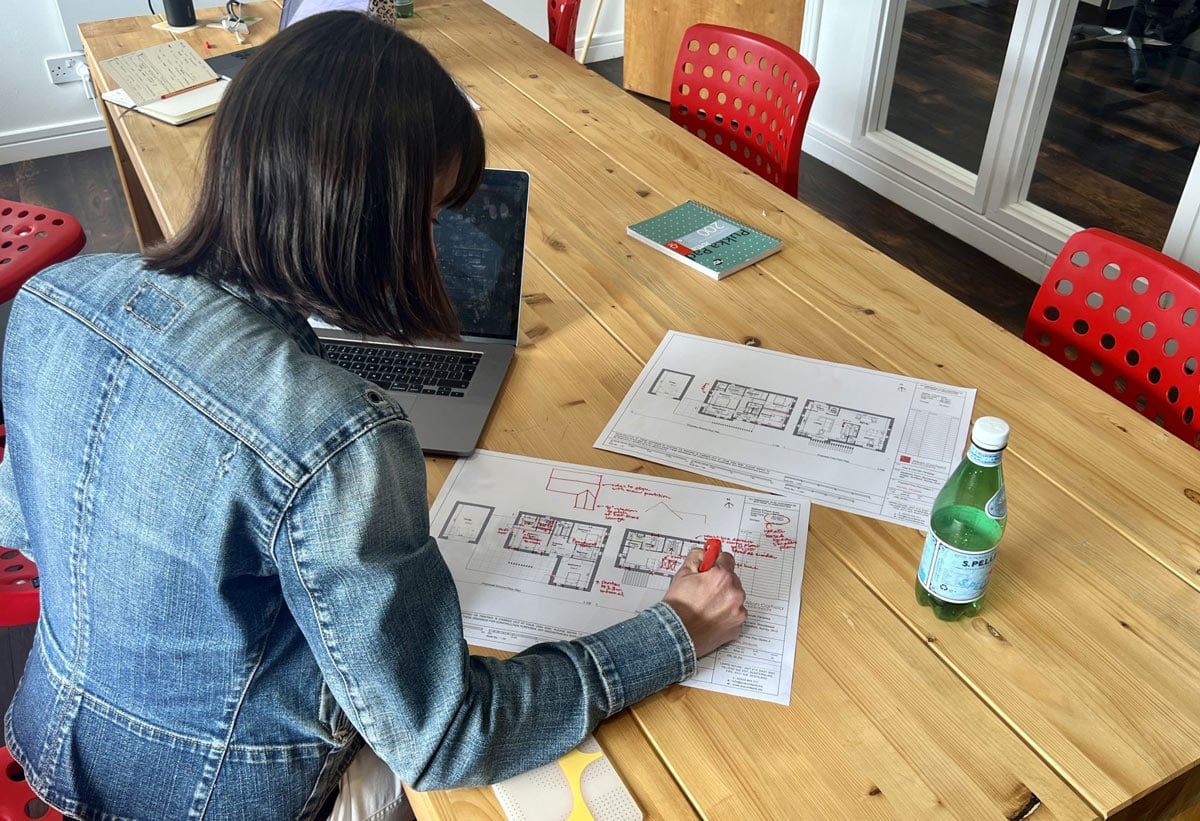
Always design with your chosen construction method in mind, as each approach offers its own efficiencies. Communicate clearly with your design team about your preferences and project goals. If you’re keen on large spans, think about how to maximise these using SIPs or other suitable construction methods. Similarly, if you opt for Insulated Concrete Forms (ICF), coordinate window locations and floor heights to align seamlessly with ICF modules. Early planning and alignment can help mitigate future challenges.
As we’ve discussed, overheating can be a concern for low-energy homes. Consider design features that help control interior temperatures, ensuring your home remains comfortable and energy-efficient.
Before moving into the planning phase, aim to have a “frozen” design. In other words, your design should be well-defined and not subject to major alterations. This stage should minimise the need for post-planning amendments, providing greater cost certainty and allowing you to focus on the technical aspects of your project.
REGS AND PRODUCTION STAGES WITH SIPS
With the initial design phase behind you and your chosen construction method in place, you’re now at the stage where your low-energy home project starts to take shape. Here’s what you can expect during the regulatory and production stages of your journey.
At this point, you’re equipped with an efficient design, and you’ve likely engaged a kit company if that’s your chosen construction route. For kit construction, specifications are honed and finalised for the major project components. However, if you’re opting for modern masonry or Sips, where roof-to-wall connections are a consideration, special attention is needed to address potential cold bridging issues.
If Passive House principles are a part of your project, you’ll need to run Passive House Planning Package (PHPP) calculations. These are performed early in the design process to validate energy performance, but they should also be revisited once you have a more specific specification in place. Additionally, SAP calculations may be required, as they are a key component of compliance with building regulations. This step ensures alignment with the regulatory framework.
The landscape of construction costs can fluctuate over time. Even within the span of several years or months, changes can occur. As a result, you and your design team should monitor these changes closely. This proactive approach ensures that the project’s design and specifications remain viable and aligned with your budget and low-energy goals.
During the regulatory and production stages, your vision takes significant steps toward becoming a reality. You’re transforming plans into tangible construction steps, with an eye on compliance, energy efficiency, and cost management. This careful balance ensures that your low-energy home project remains on track and achieves its intended objectives.
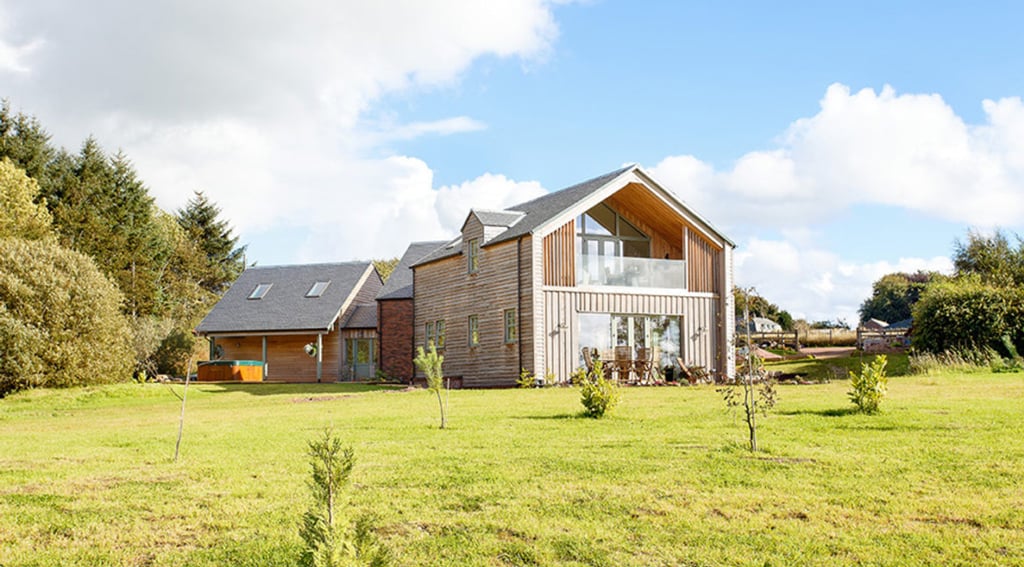
ON-SITE STAGE WITH SIPS
During the on-site phase, it’s vital to discharge planning conditions and obtain conditional approval for building regulations, ensuring compliance with local laws and regulations. Effective and transparent communication is essential among all project stakeholders, emphasising your commitment to low-energy construction.
Airtightness remains a cornerstone of energy-efficient building, and you should consistently reinforce its importance to your team. Consider scheduling toolbox talks at key project stages, particularly regarding the building’s envelope, with guidance from your design team.
Be attentive to timely adjustments and consult with your design team before implementing any changes. Their expertise can help prevent unintended consequences and keep the project on track. Meticulous attention to detail, especially regarding airtightness, is crucial for maintaining high-quality standards in your low-energy home.
Throughout the on-site phase, running proposed changes or adjustments past your design team ensures collaborative decision-making, contributing to the successful realisation of your energy-efficient dream home.
In summary, the importance of low-energy designs cannot be overstated, emphasizing the need to incorporate these considerations early in your project’s planning stages. Ensure that your entire design team is well-informed about your low-energy objectives, fostering a shared understanding of your vision.
Open lines of communication with various tradespeople to clarify your energy goals, promoting a collaborative approach to the project. Be prepared to address traditional construction details that may arise during the process, as they are inevitable.
Striving for Passivhaus standards should be a priority, and throughout the project, consistently communicate the reasons behind this choice. Make it clear to your design and building teams that your ultimate aim is to achieve a low-energy home, emphasising the significance of this goal as a collective mission.
For more Self Build advice, take a look at the learning centre or follow the link below to arrange a free initial consultation with one of our team.